Build Confidence That Your Supplier Management Process Mitigates Risk.
-
Achieve good manufacturing best practices
-
Maintain your company's quality standards
-
Enhance your understanding of the suppliers and subcontractors within your network
-
Meet requirements for FDA Part 820 and ISO 13485:2016
-
Validate suppliers and subcontractors
-
Reduce nonconformance
-
Improve purchasing controls and supplier evaluation
Download the Checklist
Get the Checklist to evaluate your supplier management process. Download it now.
Comprehensive Toolkit for Managing Your Supply Chain
Choosing the right suppliers and subcontractors is an essential step. This careful selection process is key to consistently delivering high-quality products and fulfilling your promises to customers.
With this Toolkit you'll gain:
-
Step by step Guidance with Tutorials: By following the tutorials in this vendor risk management program you can work at your own pace to assess your process. Our consultants are available if you need additional guidance with filling in the gaps in this part of your QMS - Quality Management System.
-
Consulting Expertise: With SafeLink’s assistance ensure that your supplier QMS can withstand the increasingly complex regulatory environment. We are committed to providing innovative solutions that will help your business succeed.
Essential components include:
- Identifying critical and non-critical suppliers
- Developing criteria for risk levels
- Creating evaluation forms
- Implementing complaint system
- Establishing standard operating procedures
- Developing work instructions and supporting documentation
- Consulting guidance
Have a supplier management process in place?
SafeLink offers supplier audits to help you find and address quality issues that could impact your products or business.
QMS - Supplier Management Process
This part of a Quality Management System is intended to show how the organization:
-
Ensures the adequacy of specified purchase requirements prior to communication to the supplier.
-
Evaluates and selects suppliers based on their ability to supply products in accordance with the organization's requirements.
-
Develops criteria for selection, evaluation and re-evaluation is established
-
Records the results of evaluations and any necessary actions arising from the evaluation shall be maintained. (ISO 13485 Section 7.4.1 Purchasing Process; Part 820 Section 820.50 Purchasing Data)
-
Conducts inspection and other activities necessary for ensuring that purchased product meets specified purchase requirements (ISO 13485:2016 Section 7.4.3 Verification of purchased product; FDA Part 820 Section 820.50).
-
Ensures that product which does not conform to product requirements is identified and controlled to prevent its unintended use or delivery.
-
Documents non-conforming product and the actions taken to resolve issue with supplier.
-
Determines when the organization needs to perform verification at the supplier’s premises which would notify supplier of the intended verification arrangements.
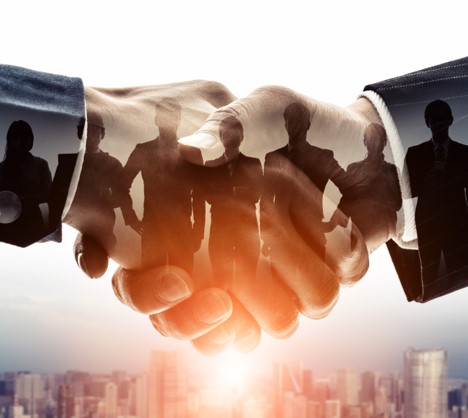
Get expert assistance with developing an effective Quality Management System.
A well-implemented QMS is an indispensable tool to drive efficiency, compliance, and competitiveness for long-term success. A QMS - Quality Management System is the cornerstone of excellence providing a structured approach to ensure consistent quality
SafeLink Consulting offers expert assistance to help your business achieve FDA compliance and develop a highly effective quality management system. Discover more about FDA Dental Regulations.
Here's how SafeLink Consulting can assist your business
Premier provider of Safety Programs and Quality Systems
-
Risk assessments and due diligence performed by safety and quality experts
-
Effective written safety and quality programs customized for your business
-
Onsite or virtual safety consulting, training, and audits to reduce risks and assist in meeting OSHA compliance
-
OSHA Outreach Trainers, ASQ Certified Quality Auditor, and CDT on staff
-
Onsite Quality Management System development and internal audits by a Certified ASQ Auditor for product or process issues
-
Guidance with an OSHA or FDA inspection or inquiry, compliance audits, and assistance in registering with FDA
Get expert assistance.
With SafeLink's support, make sure your supplier QMS is equipped to handle the ever-evolving regulatory landscape. We are dedicated to delivering creative solutions that will drive your business to success.